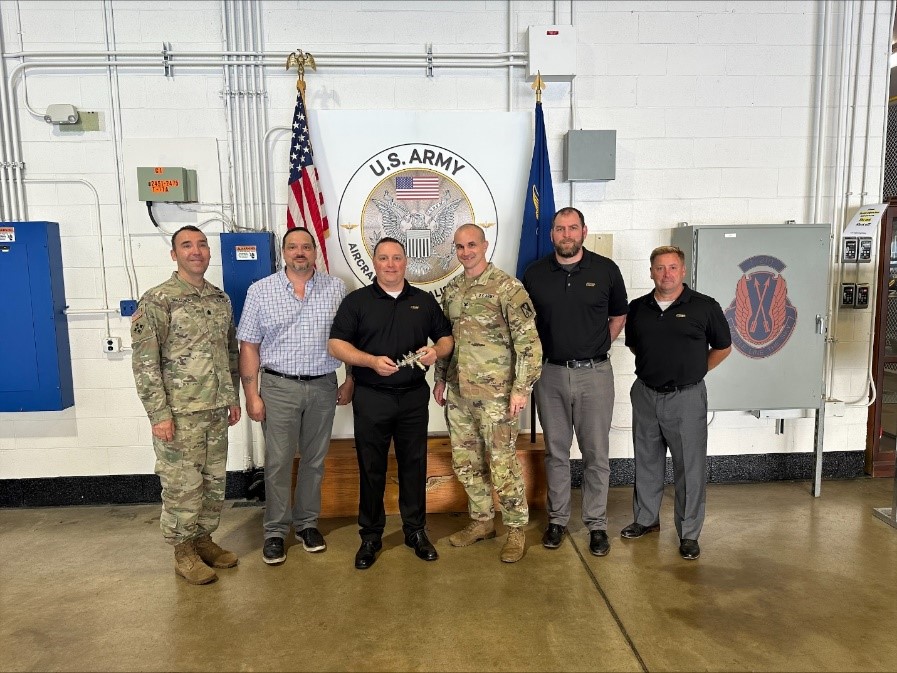
A four-year collaboration between Wichita State University’s National Institute for Aviation Research (NIAR) and the U.S. Army’s Future Vertical Lift Cross Functional Team (FVL-CFT) has led to the successful reverse engineering and production of a hydraulic ramp door actuator.
Former FVL-CFT Senior Sustainment Advisor Cindy Ponder chose this part as training aid to demonstrate the potential of advanced reverse engineering and manufacturing technology to rapidly and efficiently develop replacement parts with the same form, fit and function as the original part. This process will increase operational readiness and reduce operation and sustainment cost, allowing the Army to keep serviceable parts on the shelf to support the fleet.
“This is an exciting advancement in digital twin sustainment technology,” said Ponder. “It is truly an honor to have the opportunity to solve a problem that has a direct impact on supporting the soldier.”
The Hydraulic Ramp Door actuator was reverse-engineered at NIAR using a Northstar Imaging X3000 X-Ray computed tomography (CT) machine. NIAR engineers, in collaboration with the FVL-CFT, used the scanning data to develop a CAD model, which was then used to print the replacement part using Laser Powder Bed Fusion (LPBF) additive manufacturing technology.
“Without performing the X-Ray CT scan it would have been difficult to determine the diameter and features of the internal hydraulic fluid pocket,” said NIAR Director of Advanced Materials and Processes Royal Lovingfoss.
Internal and exterior scan data was melded to create a fully digitized CAD model. The interior design was simplified for advanced machining and extracting purposes, removing difficult machining features such as tight tolerances and threaded holes and internal support structure. Part features to be machined were designed with a 0.03-inch excess to ensure there was enough material to machine down critical features to the final required dimensions.
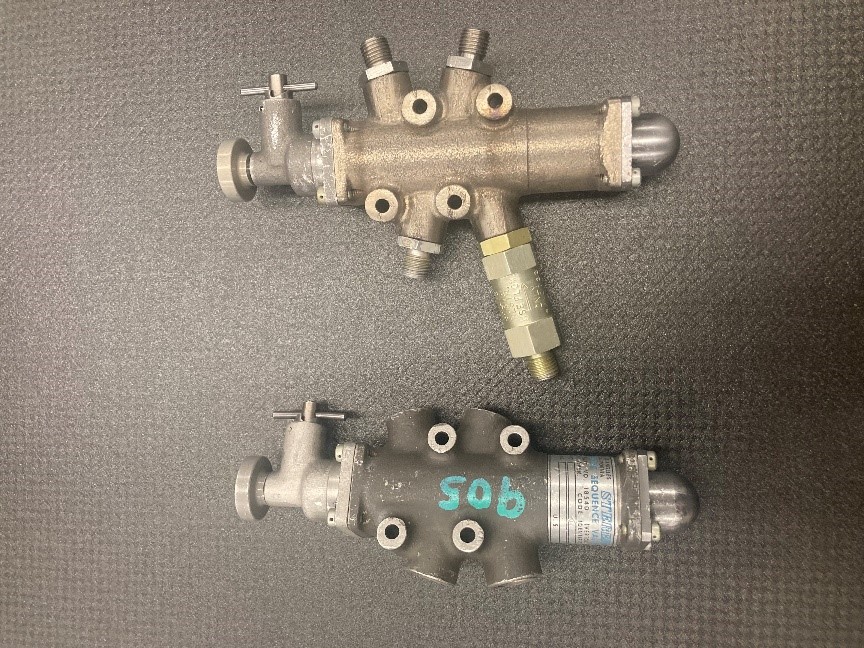
The part build layout and support structure design was developed using Materialize Magics software, and the part was fabricated from Inconel 718 material using an EOS M290 metal 3D printer.
Wire Electric Discharge Machining was used to remove the parts from the build plate. This process uses a .01-inch diameter brass wire to remove parts from the build plate with minimal material removal.
Build features are then removed and the parts were ready for final machining using 5-Axis CNC machining and programming, which ensures proper datum alignment and that all machining parameters are met.
The complex internal features were completed using special tooling designed by NIAR engineers. The custom slot cutter with an extended shank with Polycrystalline diamond inserts was developed to ensure internal slots are cut in one machine setup, and the dimensional integrity conforms to the original CAD model. Once complete, the part went through an extensive dimensional quality control process using NIAR’s Coordinate Measuring Machine.
The part was then heat-treated using a vacuum solution heat treatment up to 1950°F for one hour with argon quenching followed by precipitation hardening by heating in vacuum to 1400°F for 10 hours, and finishing with furnace cool to 1200°F – for a total of 20 heat treatment hours.
Once heat treatment concluded, the part was proof-tested to 4500 psi using a hydraulic test stand to ensure it could handle the operating pressure of 3000 psi.
The finished a hydraulic ramp door actuator replacement part was delivered to Army Team at Fort Eustis.
“The partnership of the U.S. Army Combat Capabilities Development Command Aviation & Missile Center, FVL-CFT and NIAR to support Army Aviation will enable the Army Material Command, through the Rock Island Arsenal, to use this technical data package to rapidly manufacture this part to support sustainment of the fleet,” said Ponder
“NIAR’s work in driving change in the disciplines of advance manufacturing, composites, robotics, digital engineering, digital twin, predictive maintenance and virtual reality is solving the problems of today and will have direct benefits for decades to come for the Army,” she said. “I believe that this process can expand into Missile and Space as well as Ground Combat Systems.”